In the competitive world of steel manufacturing, efficiency, reliability, and safety are paramount. As steel plants evolve to meet the demands of a global market, the need for sophisticated and integrated systems has become critical. One of the key areas where technology can drive significant improvements is power management and distribution. Substation automation, a critical component of modern industrial automation, allows steel plants to optimize their operations, and reduce downtime. Additionally, enhances overall productivity. Automation Solutions for Steel Plants are designed to address the unique challenges of the steel industry. Moreover, where maintaining a stable and reliable power supply is crucial for uninterrupted operations.
The integration of advanced Automation in Steel Industry not only ensures efficient power distribution but also plays a vital role in enhancing safety and minimizing energy losses. In this blog, we will explore how advanced substation automation solutions can optimize steel plant operations. Consequently, discuss their benefits, and examine the factors influencing the implementation and Automation Solutions for Steel Plants Cost.
The Importance of Automation in the Steel Industry
Steel production is an energy-intensive process that involves a series of complex operations. Especially, from raw material processing to the final product. Any disruption in the power supply can lead to significant production losses, equipment damage, and safety hazards. Therefore, the need for reliable and efficient power management systems in steel plants cannot be overstated.
Automation in Steel Industry has become a critical factor in improving operational efficiency and ensuring the reliability of power supply. By automating the control and monitoring of electrical substations, steel plants can achieve real-time data acquisition. Consequently, remote monitoring, and advanced protection schemes.
To increase productivity and reduce unneeded downtime, we provide Steel Plant Automation Solutions. Additionally, we teach the client’s operation and maintenance staff in our new installation. Consequently, so they can better comprehend the technology and increase the efficiency of the plant.
We offer the following Automation Solutions for Steel Plants:
- Fast Bus Transfer and Temporary Paralleling Schemes: When moving a motor bus from one source to another. A bus transfer system is meant to keep the loads connected to it operating as usual.
- Plan for load shedding: When there are mains overloads, load shedding for interruptible loads is frequently the only way to maintain industry continuity.
- Studies of Power Systems and Relay Coordination: To ensure that the system is operating safely and prevents annoying tripping. However, A relay coordination study and analysis is carried out.
- Upgrades and Retrofits of Protection Systems Using Contemporary Numerical Relays: Older relays, which are typically out of date. Moreover, should be changed in industries to prevent mishaps and facilitate plant operations.
- Meters for Monitoring Outage Losses: In an industry, outages may result in losses. It is common practice to categorize these outages as either uncontrolled (fault trip) or managed (regular shutdown).
Key Benefits of the Substation Automation Solutions for Steel Plants
Implementing Automation Solutions for Steel Plants offers a range of benefits that contribute to the overall optimization of steel plant operations. The following are some of the main benefits:
- Enhanced Operational Efficiency: Substation automation allows for real-time monitoring and control of electrical systems. Consequently, enabling steel plants to optimize power distribution and reduce energy losses.
- Improved Reliability and Safety: By integrating advanced protection and control systems, Automation Solutions for Steel Plants. It enhance the reliability of power supply and minimize the risk of electrical faults.
- Reduced Downtime: Downtime in a steel plant can be extremely costly, both in terms of lost production and equipment damage. Substation automation systems can detect and isolate faults quickly, preventing widespread outages and reducing the time needed for repairs.
- Cost Savings: While the initial Automation Solutions for Steel Plants Cost may be significant. The long-term savings in energy costs, reduced downtime, and extended equipment life make it a worthwhile investment.
- Scalability and Flexibility: Modern substation automation solutions are designed to be scalable and flexible. However, allowing steel plants to expand their operations without major disruptions. This is particularly important in an industry where demand can fluctuate, and plants need to adapt quickly to changing market conditions.
- Integration with Other Systems: Automation Solutions for Steel Plants can be integrated with other industrial automation systems, such as SCADA (Supervisory Control and Data Acquisition) and DCS (Distributed Control System).
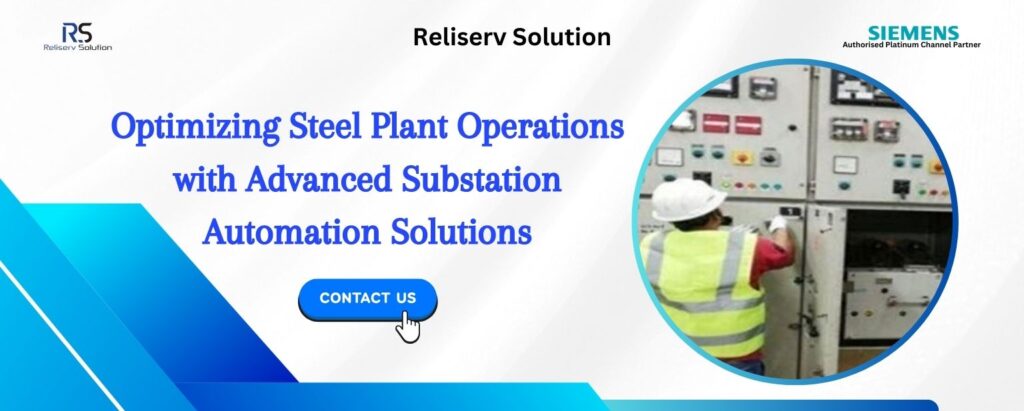
Advanced Technologies in Substation Automation in Steel Industry
The success of Automation in Steel Industry heavily relies on the implementation of advanced technologies that can handle the specific requirements of steel production. Here are some of the key technologies involved in substation automation for steel plants:
- Intelligent Electronic Devices (IEDs): IEDs are critical components of modern substation automation systems. They perform various functions such as protection, control, monitoring, and communication. In steel plants, IEDs are used to manage the distribution of electrical power, detect faults, and trigger protective actions.
- Communication Networks: Reliable and fast communication networks are essential for the real-time operation of substation automation systems. Ethernet-based communication protocols, such as IEC 61850, enable seamless data exchange between IEDs, control centers, and other devices in the network.
- Advanced Protection Schemes: Substation automation systems in steel plants incorporate advanced protection schemes that can detect and respond to electrical faults with high precision. These protection schemes are designed to minimize the impact of faults on the plant’s operations.
- Remote Monitoring and Control: Remote monitoring and control capabilities allow plant operators to manage substations from a central control room or even from off-site locations. This reduces the need for on-site personnel and enables quick response to any issues that arise.
- Data Analytics and Reporting: Automation systems generate large amounts of data that can be used for analysis and reporting. By leveraging data analytics, steel plants can gain valuable insights into their power usage patterns, identify inefficiencies, and make informed decisions to optimize their operations.
Factors Influencing Automation Solutions for Steel Plants Cost
The Automation Solutions for Steel Plants Cost can vary widely depending on several factors, including the size and complexity of the plant, the level of automation required, and the specific technologies used. Some of the main variables that affect the price of automation solutions are as follows:
- Initial Investment: The initial cost of implementing Automation Solutions for Steel Plants in India includes the purchase of hardware, software, and other equipment. This also covers the installation, configuration, and integration of the automation systems.
- Customization and Scalability: Customizing the automation solutions to meet the specific needs of a steel plant can add to the overall cost. Additionally, if the plant requires scalable solutions to accommodate future expansion, this can also impact the cost.
- Maintenance and Upgrades: Ongoing maintenance and periodic upgrades are essential to keep the automation systems running smoothly for Automation Solutions for Steel Plants in India. The cost of maintenance contracts, software updates, and hardware replacements should be factored into the overall cost.
- Training and Support: Ensuring that plant personnel are adequately trained to operate and maintain the automation systems is crucial. The cost of training programs and technical support should be considered when evaluating the total cost of ownership.
- Regulatory Compliance: Compliance with industry standards and regulations can also influence the Automation Solutions for Steel Plants Cost. Automation Solutions for Steel Plants in India may need to invest in additional equipment or software to meet regulatory requirements.
Conclusion
In conclusion, Automation Solutions for Steel Plants are essential for optimizing operations, enhancing safety, and improving the reliability of power management systems. As the steel industry continues to evolve, the need for advanced Automation in Steel Industry will only grow, making it a critical investment for steel manufacturers looking to stay competitive in the global market.
While the Automation Solutions for Steel Plants Cost may be significant, the long-term benefits, including reduced downtime, cost savings, and improved operational efficiency, make it a worthwhile investment.
For steel manufacturers in India, choosing the right Automation Solutions for Steel Plants in India is crucial. As the demand for high-quality steel continues to rise, the role of automation in the steel industry will become increasingly important, paving the way for a more efficient and sustainable future.
Reliserv Solution is an authorized supplier, distributor, and a Platinum Channel Partner of Siemens, with its headquarters situated in Mumbai, Maharashtra. Panel building is one industry that might benefit from our specialist services and solutions. Kindly contact us by email at [email protected] or by phone at +917506112097 if you require assistance or have any inquiries. To browse our collection of accessible Automation Solutions, kindly click here. Along with the well-known Substation Automation Solutions for Steel Plants.