Substation Automation Testing And Commissioning has become an essential component of modern power systems, enhancing reliability, efficiency, and remote monitoring capabilities. However, to ensure a smooth transition from traditional substations to automated ones, rigorous testing and commissioning processes must be in place. These procedures validate system performance, interoperability, and long-term operational stability.
In this blog, we will explore the best practices for substation automation testing and commissioning. We will also debunk common myths that prevent industries from adopting automation, emphasizing the benefits of integrating SCADA and automation systems into power networks.
Overview Of Substation Automation Testing and Commissioning
Substation automation involves integrating control, monitoring, and protection systems into a unified, digital framework. This is achieved using advanced Intelligent Electronic Devices (IEDs), SCADA software, and communication protocols.
Substation Automation Testing And Commissioning plays a critical role in enhancing power system efficiency, reliability, and remote monitoring capabilities. To ensure a seamless transition from traditional substations to automated systems, rigorous testing and commissioning processes are essential. These procedures validate system performance, interoperability, and operational stability before full deployment.
Testing begins with design validation, followed by Factory Acceptance Testing (FAT) to ensure compliance with industry standards like IEC 61850. On-site installation and commissioning include wiring verification, relay protection testing, and SCADA integration. Site Acceptance Testing (SAT) further confirms system functionality under real-world conditions.
Despite common myths, substation automation is now cost-effective and scalable, even for small and mid-sized industries. Automation eliminates reliance on manual operations, enabling remote monitoring, predictive maintenance, and real-time fault detection. Leading SCADA platforms like SIEMENS SICAM PAS, WinCC, GE-Alstom PaCiS, and Schneider ECO SUI facilitate seamless integration of Intelligent Electronic Devices (IEDs).
By adopting best practices in testing, training, cybersecurity, and standardization, industries can maximize automation benefits. Implementing a robust automation framework improves asset management, enhances grid stability, and reduces downtime, making it a strategic investment for the future of power systems.
Key Steps in Substation Automation Testing and Commissioning
- System Design and Engineering Validation
- Define automation architecture based on operational needs.
- Select suitable IEDs, RTUs, HMIs, and SCADA platforms.
- Ensure compliance with IEC 61850 and other industry standards.
- Pre-Installation Testing
- Conduct Factory Acceptance Tests (FAT) to verify functionality.
- Check interoperability between IEDs from different manufacturers.
- Validate communication protocols such as Modbus, DNP3, and IEC 61850.
- On-Site Installation and Testing
- Verify proper wiring and power supply connections.
- Perform loop checks to ensure data flow between field devices and SCADA.
- Test remote control capabilities from the central monitoring system.
- Protection Relay Testing
- Validate relay coordination schemes for faults and load conditions.
- Simulate real-world scenarios to check response accuracy.
- Ensure settings align with grid protection requirements.
- SCADA System Integration and Functional Testing
- Configure SCADA software to display real-time system parameters.
- Test alarms, event logging, and data storage functions.
- Verify remote access and control features for operators.
- Site Acceptance Testing (SAT) and Commissioning
- Conduct final system validation with real power flow.
- Train personnel on automation system operation and troubleshooting.
- Document test results and system configurations for future reference.
Overcoming Common Myths in Substation Automation Testing And Commissioning
Many small- and mid-sized industries hesitate to adopt substation automation due to misconceptions about cost and necessity. Let’s address these concerns.
Myth 1: Substation Automation is Too Expensive
It is commonly believed that substation automation solutions are cost-prohibitive. This misconception stems from early automation solutions that primarily catered to large utilities. However, advancements in technology have made automation solutions more accessible and cost-effective for small- and mid-sized industries.
Today, OEMs like Siemens, Schneider, GE-Alstom, and ABB offer scalable automation solutions through authorized system integrators. These integrators have expertise in designing cost-efficient systems with reduced engineering and service overheads, making automation economically viable.
Myth 2: Manual Operation is Sufficient for Our Industry
Some industries believe they can manage their power assets manually without automation. However, manual control has several limitations, especially during crises.
For example, during the COVID-19 pandemic, industries operating with limited personnel faced significant challenges in ensuring uninterrupted power supply. An automated substation enables remote monitoring and control, reducing reliance on on-site manpower. With automation, operators can monitor circuit breakers, relays, transformers, and other assets from a central location, ensuring continuous operations with minimal human intervention.
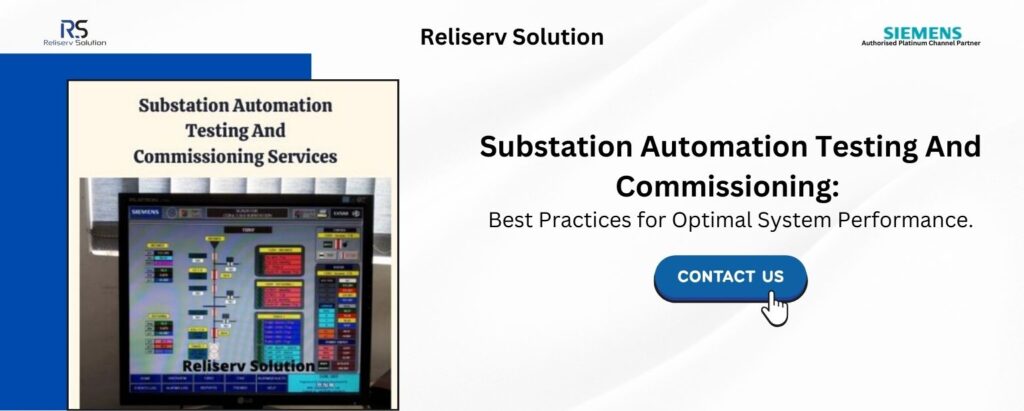
Key Benefits of Substation Automation Testing And Commissioning
Implementing a robust Substation Automation Testing And Commissioning system provides several advantages, including:
- Enhanced Reliability and Grid Stability: Automation systems continuously monitor and analyze power system parameters, enabling proactive fault detection. Automated circuit breakers and relays can react instantly to abnormalities, preventing widespread outages.
- Improved Asset Management: Automation systems provide real-time insights into equipment health. Predictive maintenance alerts allow industries to schedule timely maintenance, reducing downtime and extending asset lifespan.
- Seamless Integration with SCADA Systems: Modern substations integrate with SCADA platforms such as SIEMENS SICAM PAS, WinCC, SICAM 230, GE Alstom PaCiS, and Schneider ECO SUI. These platforms offer real-time visualization, alarm management, and remote control, ensuring streamlined operations.
- Remote Monitoring and Control: Operators can monitor and control substations from remote locations using secure communication networks. This feature is particularly useful in industries with geographically dispersed substations.
- Compliance with Industry Standards: Automated substations comply with global standards such as IEC 61850, ensuring interoperability between different manufacturers’ devices. This standardization enhances flexibility and future scalability.
Best Practices for Implementing Substation Automation Testing And Commissioning
To maximize the benefits of substation automation, industries should adopt the following best practices:
- Choose the Right Automation Partner: Select a vendor or system integrator with proven experience in SCADA integration, IED configuration, and interoperability solutions. Ensure they have expertise in the latest industry standards.
- Standardize Communication Protocols: Use industry-standard protocols such as IEC 61850, Modbus, and DNP3 to ensure seamless communication between devices from different manufacturers.
- Conduct Comprehensive Testing: Rigorous FAT and SAT procedures should be conducted to validate system performance before commissioning.
- Train Personnel: Automation systems require skilled operators for effective utilization. Conduct training sessions to familiarize staff with the SCADA interface, remote control features, and troubleshooting techniques.
- Implement Cybersecurity Measures: Substation automation systems rely on network communication, making them vulnerable to cyber threats. Implement firewalls, encrypted communication channels, and access control policies to secure critical infrastructure.
Conclusion
Substation Automation Testing And Commissioning is no longer a luxury; it is a necessity for industries seeking efficiency, reliability, and remote control capabilities. While myths about cost and necessity have persisted, modern automation solutions are now tailored for businesses of all sizes.
By following best practices in testing, commissioning, and integration, industries can unlock the full potential of substation automation. With the right approach, companies can enhance grid stability, improve asset management, and future-proof their power systems.
Investing in SCADA-integrated automation is a strategic move that ensures long-term operational efficiency while reducing dependency on manual intervention. As technology continues to evolve, businesses that embrace automation will gain a competitive edge in managing their electrical infrastructure.
With its headquarters in Mumbai, Maharashtra, Reliserv Solution is both a Siemens Authorized supplier and a Platinum Channel Partner. A variety of our specialized services and solutions are also available to the Substation Automation Testing Services Provider. If you have any queries or require assistance, please contact us by phone for Substation Automation Testing Services Cost at +917506112097 or by email at [email protected]. Click this link to see our list of all the Field Services we offer. Over the years, we have provided a wide range of additional services in addition to the well-known Study and Analysis Services.